KENENG has more than ten years of experience in manufacturing fasteners such as screws, nuts, bolts, etc., and can perform various surface treatments on them.
Common white screws mainly include electroplating white nickel, white zinc, and so on.
The process of electroplating white zinc is degreasing-cleaning-weak acid activation-electro-galvanizing-cleaning-white passivation-cleaning-drying. The difference from black zinc is that there is no over-sealing paint, and the passivation solution is also different. White passivation is a colorless and transparent zinc oxide film that contains almost no chromium, so the corrosion resistance is worse than that of black zinc, blue zinc, and color zinc.

The corrosion resistance of white zinc is better than that of white nickel, and its appearance is darker than that of white nickel.
The process of electroplating white nickel is degreasing – cleaning – weak acid activation – cleaning – copper plating bottom – activation – cleaning – nickel plating – cleaning – passivation – cleaning – drying – or sealing. The process of electroplating white nickel and electroplating black nickel is basically the same, the difference lies in the formula of the electroplating solution, without the addition of zinc sulfide.
Other Color Plated Screws
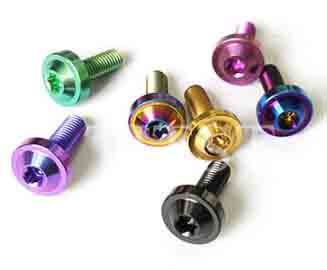
The plating of other colors mainly includes blue zinc, green zinc, colored zinc, and Dacromet.
The electroplating process of blue zinc and green zinc is roughly the same as that of white zinc. Blue zinc is a passivated zinc oxide film containing 0.5-0.6 mg/dm2 of trivalent chromium. Green passivation is due to the fact that the passivation solution contains phosphate ions, and the resulting green film is composed of chromate and phosphate.
The corrosion resistance of blue zinc is better than that of white zinc, and the corrosion resistance of green zinc is better than that of blue zinc.
Color zinc has relatively good corrosion resistance. The passivation process is: galvanizing – cleaning – 2%-3% nitric acid to emit light – cleaning – low chromium color passivation – cleaning – baking aging. Too low temperature during passivation will result in slow film formation and thin color film. The high temperature will cause the film to be thick and loose, and the adhesion will not be strong. It’s best to control around 25 degrees to ensure that you get the same color for a certain amount of time. After passivation, it needs to be baked to improve the adhesion and corrosion resistance of the film.
Dacromet
Dacromet is a new type of screw surface treatment, anti-corrosion coating with zinc powder, aluminum powder, chromic acid, and deionized water as the main components. The process flow is organic solvent degreasing – mechanical polishing – spraying – baking – secondary spraying – baking – drying.
The advantage of the Dacromet process is that the corrosion resistance is very good, but the disadvantage is that the coating is not uniform.
Comments (0)